design sheet metal forming process In this comprehensive guide, we will explore different types of sheet metal forming processes, materials used, design considerations, tooling and equipment, process steps, quality control, troubleshooting, .
According to UL (Underwriters Laboratories), a type 1 508A electrical enclosure is “an assembly incorporating two or more pieces of industrial control equipment or related control circuit .
0 · sheet metal working process pdf
1 · sheet metal stamping process pdf
2 · sheet metal processes pdf
3 · sheet metal operations with diagrams
4 · sheet metal forming process pdf
5 · sheet metal bending process pdf
6 · forming sheet metal by hand
7 · bulk deformation vs sheet metal forming
What Junction Boxes do you need for Ultegra 6870? You'll need two junction boxes. One for the rear called the B junction that connects to the derailleurs, battery and front junction. You can use either: SM-JC40 - external. SM-JC41 - internal. You'll need one for the front called the A junction that connects to the brifters and rear junction.
Sheet metal fabrication is the process of forming parts from a metal sheet by punching, cutting, stamping, and bending. 3D CAD files are converted into machine code, which controls a .
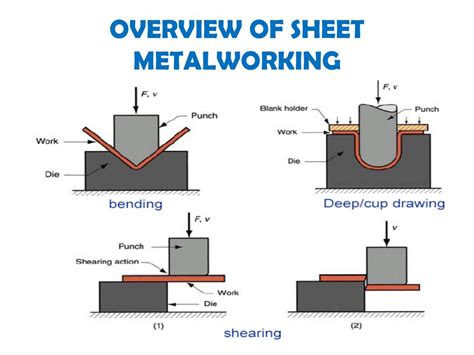
The sheet metal fabrication process consists of two main processes; forming and cutting. These two techniques work together to create the final form of any product. While cutting is a simple process, forming has further .
Starting with the 2D cutting process needed to make a blank, then exploring forming operations necessary for various sheet metal features, and finally concluding with finishing and assembly considerations as well as how to .
In this article, we’ll give you the lowdown on sheet metal forming, including the various processes, suitable materials, and its pros and cons. What is Sheet Metal Forming? Also known as sheet metal fabrication, sheet metal .
Sheet Metal Fabrication is the process of forming parts from a metal sheet by punching, cutting, stamping, and bending. 3D CAD files are converted into machine code, which controls a machine to precisely cut and form the sheets .
In this comprehensive guide, we will explore different types of sheet metal forming processes, materials used, design considerations, tooling and equipment, process steps, quality control, troubleshooting, .By an engineer with decades of practical manufacturing experience, this book is a complete modern guide to sheet metal forming processes and die design - still the most commonly used. Sheet metal forming involves several key techniques and processes, each tailored to specific applications and desired outcomes. These include: 1. Bending is a fundamental sheet metal forming process that involves ..describe different forming processes, when they might be used, and compare their production rates, costs and environmental impacts .calculate forming forces, predict part defects (tearing, wrinkling, dimensional inaccuracy), and propose solutions .explain current developments: opportunities and challenges Objectives
Sheet metal fabrication is the process of forming parts from a metal sheet by punching, cutting, stamping, and bending. 3D CAD files are converted into machine code, which controls a machine to precisely cut a flat pattern, which can be formed . Sheet metal fabrication is a comprehensive cold-working process for thin metal sheets, typically less than 6 mm in thickness. This versatile manufacturing method encompasses a wide range of operations, including shearing, blanking, bending, welding, riveting, die forming, and surface treatments. The sheet metal fabrication process consists of two main processes; forming and cutting. These two techniques work together to create the final form of any product. While cutting is a simple process, forming has further classifications, namely stamping, bending, and punching.
Starting with the 2D cutting process needed to make a blank, then exploring forming operations necessary for various sheet metal features, and finally concluding with finishing and assembly considerations as well as how to ensure your team puts out good designs that your manufacturers can understand and make at a high quality. In this article, we’ll give you the lowdown on sheet metal forming, including the various processes, suitable materials, and its pros and cons. What is Sheet Metal Forming? Also known as sheet metal fabrication, sheet metal forming uses metal sheets to make various products and components.Sheet Metal Fabrication is the process of forming parts from a metal sheet by punching, cutting, stamping, and bending. 3D CAD files are converted into machine code, which controls a machine to precisely cut and form the sheets into the final part. In this comprehensive guide, we will explore different types of sheet metal forming processes, materials used, design considerations, tooling and equipment, process steps, quality control, troubleshooting, advancements, applications, and more.
By an engineer with decades of practical manufacturing experience, this book is a complete modern guide to sheet metal forming processes and die design - still the most commonly used.
2x4 metal corner brackets
Sheet metal forming involves several key techniques and processes, each tailored to specific applications and desired outcomes. These include: 1. Bending is a fundamental sheet metal forming process that involves deforming a metal sheet around a straight axis to create angular or curved shapes.
.describe different forming processes, when they might be used, and compare their production rates, costs and environmental impacts .calculate forming forces, predict part defects (tearing, wrinkling, dimensional inaccuracy), and propose solutions .explain current developments: opportunities and challenges ObjectivesSheet metal fabrication is the process of forming parts from a metal sheet by punching, cutting, stamping, and bending. 3D CAD files are converted into machine code, which controls a machine to precisely cut a flat pattern, which can be formed .
sheet metal working process pdf
Sheet metal fabrication is a comprehensive cold-working process for thin metal sheets, typically less than 6 mm in thickness. This versatile manufacturing method encompasses a wide range of operations, including shearing, blanking, bending, welding, riveting, die forming, and surface treatments. The sheet metal fabrication process consists of two main processes; forming and cutting. These two techniques work together to create the final form of any product. While cutting is a simple process, forming has further classifications, namely stamping, bending, and punching.Starting with the 2D cutting process needed to make a blank, then exploring forming operations necessary for various sheet metal features, and finally concluding with finishing and assembly considerations as well as how to ensure your team puts out good designs that your manufacturers can understand and make at a high quality.
In this article, we’ll give you the lowdown on sheet metal forming, including the various processes, suitable materials, and its pros and cons. What is Sheet Metal Forming? Also known as sheet metal fabrication, sheet metal forming uses metal sheets to make various products and components.Sheet Metal Fabrication is the process of forming parts from a metal sheet by punching, cutting, stamping, and bending. 3D CAD files are converted into machine code, which controls a machine to precisely cut and form the sheets into the final part. In this comprehensive guide, we will explore different types of sheet metal forming processes, materials used, design considerations, tooling and equipment, process steps, quality control, troubleshooting, advancements, applications, and more.By an engineer with decades of practical manufacturing experience, this book is a complete modern guide to sheet metal forming processes and die design - still the most commonly used.
sheet metal stamping process pdf
sheet metal processes pdf
A1S CNC Router. Our A1S are our entry level 8ftx4ft CNC routers. Even though .
design sheet metal forming process|sheet metal stamping process pdf