closed hem sheet metal Some hems are closed, which means that the inside bend radius is zero. The hem’s cross-section resembles a U if its radius is bigger than zero. The hem has one curve rather than two, in . $468.99
0 · what is sheet metal hemming
1 · sheet metal roller hemming
2 · sheet metal hems types
3 · sheet metal hemming machine
4 · sheet metal heming angle
5 · sheet metal hem forms
6 · sheet metal die hemming
7 · open hem sheet metal
Get the best deals on White House Black Market Black Jeans for Women when you shop the largest online selection at eBay.com. Free shipping on many items | Browse your favorite brands | affordable prices.
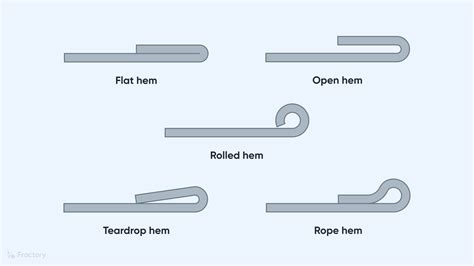
what is sheet metal hemming
The four most common types of sheet metal hems used by Approved Sheet Metal are closed hem, teardrop hem, open hem, and rolled .Some hems are closed, which means that the inside bend radius is zero. The hem’s cross-section resembles a U if its radius is bigger than zero. The hem has one curve rather than two, in .Hemming and seaming are two similar metalworking processes in which a sheet metal edge is rolled over onto itself. Hemming is the process in which the edge is rolled flush to itself, while a seam joins the edges of two materials. Hems are commonly used to reinforce an edge, hide burrs and rough edges, and improve appearance. The four most common types of sheet metal hems used by Approved Sheet Metal are closed hem, teardrop hem, open hem, and rolled hem. What are the material limitations for closed hems? Closed hems work best with material thicknesses of .040"-.125".
In a flat or closed hem, the part of the edge that bends sits completely flush over the rest of the metal sheet. The angle between the returning flange and the sheet metal is 180 degrees. The inside radius is zero and thus, there is no .Some hems are closed, which means that the inside bend radius is zero. The hem’s cross-section resembles a U if its radius is bigger than zero. The hem has one curve rather than two, in contrast to the U-channels’ two bends.Hemming and seaming are two similar metalworking processes in which a sheet metal edge is rolled over onto itself. Hemming is the process in which the edge is rolled flush to itself, while a seam joins the edges of two materials. [1] Hems are commonly used to reinforce an edge, hide burrs and rough edges, and improve appearance. [1]
Sheet metal hemming is a manufacturing process that folds metal edges to reinforce strength and safety. It reduces sharpness and enhances aesthetics, often used in automotive, aerospace, and consumer goods industries. Let’s explore the complete process, tools, benefits, and challenges of sheet metal hemming. What is Sheet Metal Hemming?Sheet metal hemming is a unique technique that involves folding the edge of sheet metal back on itself to create a double thickness. This process adds durability and strength to the part but eliminates sharp edges. A closed hem is a total flush in which the sheet metal is rolled or bent on itself. Although there may be some downsides with materials. This sheet hem type is highly compatible with the material bearing thickness range of 0.040 – 0.125 inches. Sheet metal hemming is a type of sheet metal fabrication in which the thin sheet is bent and folded onto itself. The bent can have a closed shape, completely touching the metal surface, or be open with a slight cavity in between. The primary purpose of hemming is to add structural strength and durability.
Closed hems are mostly used in metal cabinets, enclosures and car body panels. They create a tight seal, give superior edge strength and eliminate sharp edges. These hems are particular types of hems characterized by their different teardrop-shaped edges.Hemming is essential to turn the rough edges on the sheet metal parts into neater edges. Here are the benefits of this process: Applying a hemming procedure on your sheet metal materials can help improve the aesthetics of the final product. Hemming edges are even more tidy compared to the un-hemmed edges. The four most common types of sheet metal hems used by Approved Sheet Metal are closed hem, teardrop hem, open hem, and rolled hem. What are the material limitations for closed hems? Closed hems work best with material thicknesses of .040"-.125".
In a flat or closed hem, the part of the edge that bends sits completely flush over the rest of the metal sheet. The angle between the returning flange and the sheet metal is 180 degrees. The inside radius is zero and thus, there is no .Some hems are closed, which means that the inside bend radius is zero. The hem’s cross-section resembles a U if its radius is bigger than zero. The hem has one curve rather than two, in contrast to the U-channels’ two bends.
Hemming and seaming are two similar metalworking processes in which a sheet metal edge is rolled over onto itself. Hemming is the process in which the edge is rolled flush to itself, while a seam joins the edges of two materials. [1] Hems are commonly used to reinforce an edge, hide burrs and rough edges, and improve appearance. [1]
Sheet metal hemming is a manufacturing process that folds metal edges to reinforce strength and safety. It reduces sharpness and enhances aesthetics, often used in automotive, aerospace, and consumer goods industries. Let’s explore the complete process, tools, benefits, and challenges of sheet metal hemming. What is Sheet Metal Hemming?

Sheet metal hemming is a unique technique that involves folding the edge of sheet metal back on itself to create a double thickness. This process adds durability and strength to the part but eliminates sharp edges.
A closed hem is a total flush in which the sheet metal is rolled or bent on itself. Although there may be some downsides with materials. This sheet hem type is highly compatible with the material bearing thickness range of 0.040 – 0.125 inches. Sheet metal hemming is a type of sheet metal fabrication in which the thin sheet is bent and folded onto itself. The bent can have a closed shape, completely touching the metal surface, or be open with a slight cavity in between. The primary purpose of hemming is to add structural strength and durability. Closed hems are mostly used in metal cabinets, enclosures and car body panels. They create a tight seal, give superior edge strength and eliminate sharp edges. These hems are particular types of hems characterized by their different teardrop-shaped edges.
sheet metal roller hemming

collector box thunder junction
Considering a gray metal roof? We go over the most popular gray shades for roofs and the siding colors they pair with best. Plus, check out our pictures for design inspiration.
closed hem sheet metal|sheet metal hemming machine