sheet metal design guidelines Learn the basics and guidelines for designing sheet metal parts with different processes, such as forming, laser cutting and turret press. Find out the tolerances. I'm set on 42 or 46 wide units, built by Craftsmen [ 42"] or Milwaukee [ 46"] . Craftsman made in US, 18-20 gauge. Milwaukee made in Vietnam, 20" but has higher weight capacity. Without taking the drawers out to check construction build, it's hard to make a decision.
0 · sheet metal practice drawings pdf
1 · sheet metal pattern layout methods
2 · sheet metal design practice pdf
3 · sheet metal design handbook pdf
4 · sheet metal design guidelines pdf
5 · sheet metal design calculations pdf
6 · sheet metal calculations pdf
7 · basics in sheet metal design
In most cases today, homeowners hang the decorative old-looking metal stars on their homes simply because they enjoy and like them. Usually they are 5-pointed and come in various sizes. Sometimes they are hung on the porch wall.
Learn how to design good sheet metal parts for press bending with material selection, bend radius, hole diameter, grain orientation, and other guidelines. See examples and formulas for sheet metal design and avoid common failures and deformations.Sheet metal bending is a forming operation where sheets are deformed plastically to .
It helps designers in sheet metal product design because designers design parts .Learn the basics and guidelines for designing sheet metal parts with different processes, such as forming, laser cutting and turret press. Find out the tolerances.Design Guidelines: Sheet Metal Fabrication Our basic guidelines for sheet metal fabrication include important design considerations to help improve part manufacturability, enhance cosmetic appearance, and reduce overall .
If you design sheet metal parts, you may know that bend relief is a notch cut made into the . Continuing our focus on sheet metal forming, this issue of DFM guidebook focuses on design guidelines for bend relief parameters, distance between holes and bends and offset bend material when a bend is made close to an edge. 2. cold rolled sheet hot rolled sheet Galvanised sheet cold rolling can be rolled with 0.007mm metal aluminum foil At present, the thinnest hot- rolled strip can be rolled out with a steel strip of about 0.78mm Hot-dip . 1. Selection of Sheet Metal Materials. Sheet metal materials are the most commonly used materials in the structural design of communication products. Understanding the comprehensive performance of materials and the correct material selection have an important impact on product cost, product performance, product quality, and processability.. Selection .
Sheet metal design skills are a crucial tool in any engineer’s toolbox, but given how little attention sheet metal design gets in academia, most skills are learned on the job. . Guidelines are not useful in these cases as the material response is geometry specific . Sheet Metal fabrication is the building of metal structures by cutting, bending, and assembling processes. It is a value added process that involves the construction of machines and structures from various raw materials. This guide will help you to understand sheet metal product design tips and fabrication techniques. Metal. MetalworkingMETAL STAMPING DESIGN GUIDE. 452 Twin Lakes Rd North Branford, CT 06471 www.esict.com Phone: 800-486-5546 Fax: 800-486-2825 2 . Burr allowance is generally 10% of the thickness of the sheet material. To minimize instances and severity of burrs, avoid sharp corners and complex cutouts when possible. When such factors cannot
Get an overview to sheet metal fabrication from the different types of sheet metal fabrication, to design best practices, materials, finishings and fastenings. 20% off your first order. Save up to ,000/€1,000. Ends 30 Nov 2024. . Good sheet metal design goes beyond basic guidelines and considers the type of sheet metal fabrication process .
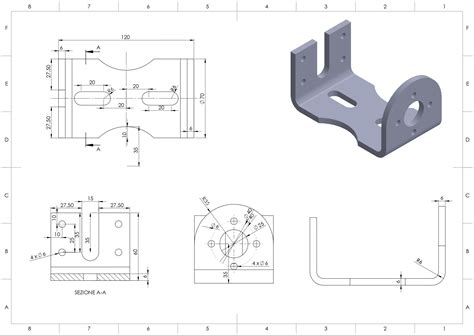
sheet metal practice drawings pdf
Sheet Metal Design Guidelines. Material Selection & Specification. The first step of designing a sheet metal component is the selection of material. Over-specifying your material can add significant costs to your component. Using standard materials will help control costs and lead times. Often times it’s far more economical to increase the . This article will provide a series of key sheet metal design and fabrication guidelines to help engineers and designers understand how to maximize the use of the characteristics of metal sheets, ensuring the feasibility of .Welcome to Kreatorzone! On this sheet metal design series you will find the recommended Common sheet metal design guidelines explained in 5 minutes. Some of . In the original design, the sheet metal required two separate bending processes. However, in the improved design, the sheet metal only needs one bending process to form the two sides at the same time. It is important to keep in mind that the more complex the bending process for the sheet metal, the higher the amount of material waste that may .
*Please use these numbers as sheet metal design guidelines only and always check with your fabricator for their recommendations before completing your design. Considerations for Sheet Metal Post-processing. Welding. Welding preparation is a critical step, especially for certain materials that require pre-welding processes like grinding. The . Designing sheet metal parts requires attention to detail to ensure the parts are manufacturable, cost-effective, and functional. Here are comprehensive guidelines to follow: Material Selection Choose the Right Material: Select materials based on required properties such as strength, corrosion resistance,.
Sheet Metal Design Guidelines – Download the free eBook. Winning in today’s dynamic marketplace requires more than just creating innovative product designs. To succeed, companies must also focus on efficient manufacturing within budget and schedule targets. The discipline of Design for Manufacturing (DFM) intends to aid designers in doing .
It also outlines various sheet metal processes like bending, forming, stamping and piercing. It provides guidelines for dimensional tolerances, factors that affect design like minimum distances between holes and bends. It defines . E.g. In the case of the Aerospace industry, the bend radius is greater than the standard bend radius of the sheet metal of the same thickness. Bend radius must be greater than 1 mm or equal to the thickness of the sheet, .No single design tip can cover all the sheet metal mistakes we’ve seen, but this “best of” collection is a start. Take a look at our sheet metal design guidelines to keep you moving in the right direction. For additional help, feel free to contact a Protolabs applications engineer at 877-479-3680 or [email protected].summary of important design guidelines for Sheet Metal. . Welcome to another issue of the DFM Guidebook. We highly feedback for our previous issues. Please continue sending us your comments, suggestions and ideas for subsequent issues. This week, our DFM experts provide you a comprehensive .
Sheet Metal Design Guidelines 2024-08-16 2024-08-16 Jiatong China Sheet Metal Fabrication Companies, China Sheet Metal Fabrication Factory, China . These guidelines help ensure that your sheet metal design is both manufacturable and functional while controlling costs.A DEFINITIVE GUIDE TO DESIGN FOR MANUFACTURING SUCCESS 4 . We hope you are finding the DFM Guidebook informative and worthy of your continued In this issue, we cover design guidelines that can help optimize features such as embosses, lip and extruded form in a sheet metal forming process. Embossing is a sheet metal forming process Sheet metal design guidelines. Mufaddal Rasheed Author. Sep 21, 2024 | Explore the various design guidelines to be followed for effective sheet metal design in product design. Essential principles that ensure the creation of functional, manufacturable, and cost-effective sheet metal parts. These guidelines encompass various aspects of design . Understanding the Basics of Sheet Metal Design. Sheet metal design requires creating parts and assemblies from flat sheets of metal, which are then shaped or formed into desired shapes by such operations as cutting, stamping or bending. Key principles include understanding material properties, tolerances, and various manufacturing methods.
Designing for sheet metal fabrication requires consideration of material properties, fabrication processes, and the capabilities of manufacturing equipment. Adhering to proper design guidelines helps in reducing costs, minimizing errors, and ensuring that the parts can be easily manufactured. Below are key sheet metal fabrication design .The sheet metal design process involves conceptualizing, drawing, and creating detailed plans for cutting, shaping, and joining metal. . and adhering to design guidelines are essential to avoid early mistakes. Can CAD software help with the Sheet Metal Design Process? The CAD software provides powerful tools to design, modify, and analyze .
During the design phase, sheet metal design guidelines focus on the following five parameters. Material Selection. Material characteristics play a crucial role in determining the suitable cutting process for a specific material. For example, aluminum is generally easier to cut than steel due to its relative strength and durability.Sheet metal design guidelines are followed to ensure quality, low cost, and time efficiency. Key guidelines include recommended minimum bend radii equal to the material thickness, minimum bend/flange lengths of 3x thickness plus bend radius, and minimum hole diameters of the material thickness or 2x thickness for harder materials. Maintaining proper distances between features, .

sheet metal pattern layout methods
Need extra juice for your equipment? A power distribution box can help. It distributes power safely from the source to other devices you need. A portable power distribution unit can be used to efficiently deliver power to all the equipment you're using so that you can get back to business. Shop with confidence!
sheet metal design guidelines|sheet metal pattern layout methods