bend angle in sheet metal Specify the Bend Angle: • Input the required bend angle in degrees. • The tool will compute the arc length, bend allowance, and bend deduction, essential for determining material requirements and tooling setup. To weld sheet metal with solid wires, use electrode positive (EP, or reverse polarity). Don’t attempt to weld thin materials like sheet metal with flux-cored wires, which put more heat into the base metal. Forget the larger 1/8 .
0 · sheet metal bending techniques
1 · sheet metal bending directions
2 · sheet metal bending diagram
3 · sheet metal bending chart
4 · sheet metal bending angle formula
5 · sheet metal bending angle chart
6 · sheet metal bend
7 · how to calculate sheet metal bending
Understanding the different electrical box types and their uses is crucial for anyone involved in electrical work or home improvement projects. In this comprehensive guide, we will .
Right Angle: A bend equal to 90 °. Right angles are the most common feature found in most sheet metal fabrication. Tonnage charts, Bend Deduction, Bend Allowance and other forming calculations and charts often refer to a 90° bend. .
stainless steel pharmacy cabinet
Specify the Bend Angle: • Input the required bend angle in degrees. • The tool will compute the arc length, bend allowance, and bend deduction, essential for determining material requirements and tooling setup.This Komaspec guide provides an overview of the main sheet metal bending processes, the advantages and disadvantages of each, basic design considerations with sheet metal bending . You can derive the Bend Allowance (BA) by using the K , Bend Radius (R), Bend Angle (A) and Material Thickness using the formula below. BA=Pi*(R+K*T)*A/180. In this formula: K represents the K-factor. BA is the .
Neutral Axis: When a sheet of metal is bent, the material on the outside of the bend stretches, while the material on the inside compresses. The neutral axis is an imaginary line within the material that remains at a constant .Understanding the basics is critical to calculating bend allowance. This is a step-by-step guide. First, you need to determine the radius and bend angle. Use the following formula: Bend . You can find your bend allowance with the following formula: (π/180) x B x (IR + K x MT) = bend allowance (BA), where B is the angle complementary to your desired bend angle (1 to 180 degrees), MT is the .
Setting the correct bend angle and radius is crucial in sheet metal bending. The bend angle is typically programmed into the bending machine, like a CNC press brake, ensuring precision in each bend. The bend radius, on the other hand, .
Sheet Metal Bending Calculation. Bend Allowance (BA) BA = [(0.017453 × Inside radius) + (0.0078 × Material thickness)] × Bend angle, which is always complementary. The length of the neutral axis is calculated as a bend allowance, taken at .
Right Angle: A bend equal to 90 °. Right angles are the most common feature found in most sheet metal fabrication. Tonnage charts, Bend Deduction, Bend Allowance and other forming calculations and charts often refer to a 90° bend. This type .
Specify the Bend Angle: • Input the required bend angle in degrees. • The tool will compute the arc length, bend allowance, and bend deduction, essential for determining material requirements and tooling setup. Bending is one of the most common sheet metal fabrication operations. Also known as press braking , flanging, die bending, folding and edging , this method is used to deform a material to an angular shape.This Komaspec guide provides an overview of the main sheet metal bending processes, the advantages and disadvantages of each, basic design considerations with sheet metal bending and material selection information.
You can derive the Bend Allowance (BA) by using the K , Bend Radius (R), Bend Angle (A) and Material Thickness using the formula below. BA=Pi*(R+K*T)*A/180. In this formula: K represents the K-factor. BA is the bend allowance. A is the bend angle. R . Neutral Axis: When a sheet of metal is bent, the material on the outside of the bend stretches, while the material on the inside compresses. The neutral axis is an imaginary line within the material that remains at a constant length during bending. The bend allowance is calculated based on the position of this neutral axis.
Understanding the basics is critical to calculating bend allowance. This is a step-by-step guide. First, you need to determine the radius and bend angle. Use the following formula: Bend allowance = (p/180 x Bend angle x (Radius x K-Factor + Thickness). Angle is a critical component in calculating bend allowance. You can find your bend allowance with the following formula: (π/180) x B x (IR + K x MT) = bend allowance (BA), where B is the angle complementary to your desired bend angle (1 to 180 degrees), MT is the thickness of the material, IR is the inside radius, and K is the K-factor.Setting the correct bend angle and radius is crucial in sheet metal bending. The bend angle is typically programmed into the bending machine, like a CNC press brake, ensuring precision in each bend. The bend radius, on the other hand, depends . Sheet Metal Bending Calculation. Bend Allowance (BA) BA = [(0.017453 × Inside radius) + (0.0078 × Material thickness)] × Bend angle, which is always complementary. The length of the neutral axis is calculated as a bend allowance, taken at .
Right Angle: A bend equal to 90 °. Right angles are the most common feature found in most sheet metal fabrication. Tonnage charts, Bend Deduction, Bend Allowance and other forming calculations and charts often refer to a 90° bend. This type .
Specify the Bend Angle: • Input the required bend angle in degrees. • The tool will compute the arc length, bend allowance, and bend deduction, essential for determining material requirements and tooling setup.
sheet metal bending techniques
Bending is one of the most common sheet metal fabrication operations. Also known as press braking , flanging, die bending, folding and edging , this method is used to deform a material to an angular shape.This Komaspec guide provides an overview of the main sheet metal bending processes, the advantages and disadvantages of each, basic design considerations with sheet metal bending and material selection information.You can derive the Bend Allowance (BA) by using the K , Bend Radius (R), Bend Angle (A) and Material Thickness using the formula below. BA=Pi*(R+K*T)*A/180. In this formula: K represents the K-factor. BA is the bend allowance. A is the bend angle. R .
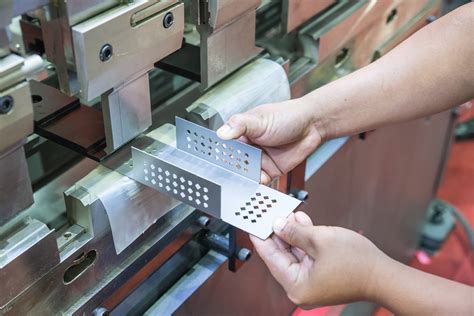
Neutral Axis: When a sheet of metal is bent, the material on the outside of the bend stretches, while the material on the inside compresses. The neutral axis is an imaginary line within the material that remains at a constant length during bending. The bend allowance is calculated based on the position of this neutral axis.Understanding the basics is critical to calculating bend allowance. This is a step-by-step guide. First, you need to determine the radius and bend angle. Use the following formula: Bend allowance = (p/180 x Bend angle x (Radius x K-Factor + Thickness). Angle is a critical component in calculating bend allowance. You can find your bend allowance with the following formula: (π/180) x B x (IR + K x MT) = bend allowance (BA), where B is the angle complementary to your desired bend angle (1 to 180 degrees), MT is the thickness of the material, IR is the inside radius, and K is the K-factor.
sheet metal bending directions
In this post, we’ll discuss the various types of electrical boxes and their uses so you can make an informed decision about your next electrical project. 1. Round Pan Electrical Box. Round pan electrical boxes are circular and are commonly used for ceiling fixtures such as chandeliers, pendant lights, and smoke detectors.
bend angle in sheet metal|sheet metal bending directions