sheet metal parts design guidelines These basic sheet metal fabrication guidelines include important design considerations to help improve part manufacturability, enhance cosmetic appearance, and reduce overall production time. Basic Principles The standard sheet metal gauge range begins at 30 on the thin end and drops down to 7 at the thicker end of the scale. However, the actual thickness and corresponding gauge will differ depending on the type of metal.
0 · sheet metal practice drawings pdf
1 · sheet metal pattern layout methods
2 · sheet metal layout techniques
3 · sheet metal design guideline pdf
4 · sheet metal design calculations pdf
5 · sheet metal calculations pdf
6 · sheet metal bending guide pdf
7 · basics in sheet metal design
Can anyone tell me what this small metal piece is for on the iPhone XR, and what it does? I managed to break it while unscrewing one of the screws, the arrow is to show where it sheared off at. My rear camera and flashlight no longer work.
sheet metal practice drawings pdf
Sheet metal design guidelines are followed for sheet metal enclosure and part design to ensure the first time right product and reduce cost.
Sheet metal bending is a forming operation where sheets are deformed plastically to .
Whereas manufacturers provide sheet metal materials in gauges. We will keep .These basic sheet metal fabrication guidelines include important design considerations to help improve part manufacturability, enhance cosmetic appearance, and reduce overall production time. Basic Principles
All sheet metal parts come with the requirement of having consistent width, which limits some of its applications. But ensures that the resulting part is able to fulfill the requirements of durability and longevity. .Sheet Metal Material Thickness Range. Because sheet metal parts are manufactured from a single sheet of metal, the part must maintain uniform wall thickness. Sheet metal thickness ranges from 0.024 in. (0.609mm) to 0.250 in. . Sheet metal fabrication design guide with tips and best practices on designing sheet metal parts for processing via laser cutting and precision CNC bending. Search Now. Popular search terms. Contract Manufacturing .The axis stop is conventionally produced out of a welded construction with a semi-finished product and milled parts. The many work steps are both time-consuming and cost-intensive. The new design made of two sheet parts reduces the number of parts and thus the joining processes and material usage.
sheet metal pattern layout methods
Sheet metal fabrication design guide with tips and best practices on designing sheet metal parts for processing via laser cutting and precision CNC bending. Search Now. Popular search terms. Contract Manufacturing . *Please use these numbers as sheet metal design guidelines only and always check with your fabricator for their recommendations . Sheet metal design.pptx - Download as a PDF or view online for free . Bend radius guidelines are as follows: For most materials, the minimum inner radius should be at least 1 material thickness. . Spot welding and seam welding are two very popular methods used for sheet metal parts. Spot welding is primarily used for joining parts that .Piercing is a common metal stamping process and ideal for forming holes and slots fully enclosed within the edges of a part. There are a number of factors to consider when designing stamped metal parts with holes to ensure proper manufacturing and functionality. Hole Diameter The minimum diameter of any hole should be 1.2x the material thickness
Sheet metal parts are manufactured from single sheet of metal, so the part must contain a uniform wall thickness. Hansen sheet metal is capable of laser cutting parts with maximum thickness: *General purposed guideline only, please contacts Hansen for any special request. Aluminum 3/8" thick Steel 3/4" thick 3. Bending of Sheet Metal Parts. You can read this post to learn every detail about sheet metal bending. 4. Structural Form of Nuts and Screws on Sheet Metal Parts Riveted nut. Common forms of riveted nuts are self-clinching standoff, self-clinching nut, anchor rivet nut, pull rivet nut, and floating rivet nut. Self-clinching standoff 10. 10 10 CONFIDENTIAL Metal Stamping manufacturing is the process of creating metal parts by applying extreme pressure to a blank piece on metal and forming the metal into a desired shape Corners should have a minimum radius of 0.5 x material thickness or 0.4 mm (0.016in) whichever is greater. Sharper corners can be produced but at a greater die .
This article will provide a series of key sheet metal design and fabrication guidelines to help engineers and designers understand how to maximize the use of the characteristics of metal sheets, ensuring the feasibility of the design and the efficiency of fabrication. . When producing sheet metal parts, it typically involves multiple .
Explore the various design guidelines to be followed for effective sheet metal design in product design. Essential principles that ensure the creation of functional, manufacturable, and cost-effective sheet metal parts. Another sheet metal design consideration for hardware that needs to be made is the timing of installation in the fabrication process. . Sheet Metal Design Guidelines: Designing Sheet Metal Parts. 11/1/2023. Design for Manufacturability. Design Tips for Stamping Parts with Progressive Dies. 5/6/2020. Mastering sheet metal design is key to achieving both precision and efficiency in manufacturing sheet metal parts. By incorporating Design for Manufacturing (DFM) principles, you can streamline production, reduce costs, and maintain high-quality standards. Whether you’re working with steel, aluminum, or copper, understanding the nuances of sheet metal processing .
Basics of Sheet Metal Design. Sheet metal design refers to creating components or parts from flat sheets of metals through cutting, bending, and assembling. Material selection, thickness, bend radius, and manufacturing processes are key considerations. The main goal is to make functional parts while reducing waste and production costs . Below are some tips and guidelines for designing sheet-metal parts. If you follow the design advice and maintain the tolerances expressed in this article, you are more likely to end up with parts .
Designing for sheet metal fabrication requires consideration of material properties, fabrication processes, and the capabilities of manufacturing equipment. Adhering to proper design guidelines helps in reducing costs, minimizing errors, and ensuring that the parts can be easily manufactured. Below are key sheet metal fabrication design .As sheet metal parts are fabricated from one sheet of metal, the part must maintain uniform wall thickness throughout. We recommend a sheet metal thickness range between 0.5-10 mm (0.02-0.394 in) for laser cutting and 0.5-6 mm (0.02-0.236 in) for bending.
Guidelines for Sheet Metal Fabrication Design As mentioned earlier, sheet metal fabrication design requires attention to specific requirements that vary based on the overall product design. Simple products may have fewer requirements, while intricate geometries may necessitate additional processes for market readiness.
sheet metal layout techniques
E.g. In the case of the Aerospace industry, the bend radius is greater than the standard bend radius of the sheet metal of the same thickness. Bend radius must be greater than 1 mm or equal to the thickness of the sheet, whichever is greater. The Minimum Bend Radius Guidelines avoids fracturing and distortion of the sheet metal under design.Learn the Basics of SHeet metal Design, Design guidelines with projects and case studies. Enroll in Course. Course Summary. This course covers the essential basic theoretical and practical knowledge required for Designing Sheet metal parts. - The common processes - Materials and the properties which matter for design - Comparison between . Welcome to Kreatorzone! On this sheet metal design series you will find the recommended Common sheet metal design guidelines explained in 5 minutes. Some of .Sheet Metal Design Guidelines eBook [Download] . Engineers commonly default to using steel hardware for their custom sheet metal parts—and it’s easy to understand why. Steel hardware is the cheapest and most ubiquitous option. If you have a steel part or a part that will be powder coated or zinc plated, steel hardware is a viable solution .
Custom Cut Sheet Metal Parts. Custom sheet metal manufacturing entails the formation of a product from sheets. By employing sophisticated techniques, the metal sheets are shaped, curved, shaped, and combined to shape a product. . DFM Guidelines For Sheet Metal Design. Design for Manufacturability (DFM) is a virtual design concept intended to . JIATONG XJ was found in March 2011, situated in humen town, with a plant area of 8200 square meters, one of China’s professional precison sheet metal manufacturer over 10 years.Offerring you One-stop integrated ODM& OEM manufacturing solutions and services including sheet metal machining, welding, painting, silkscreen, assembly.etc, from primary . Implement design guidelines and tolerance specifications tailored for sheet metal production. . The grain structure of metal sheets is crucial for preventing cracks in sheet-metal parts with lugs or tabs cut on three sides and bent inward or outward, where other components are often attached. Engineers modeling such parts must grasp the grain .Design Guide: Sheet Metal Fabrication We've compiled our best design tips into this guide to help you understand the sheet metal fabrication process, important design considerations for optimizing your parts for manufacturing, and information about Xometry's sheet metal services.
sheet metal design guideline pdf
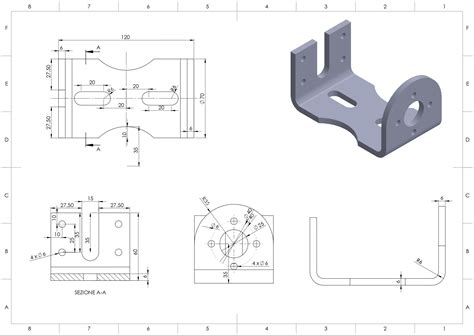
precision grinding part manufacturer
This guide will help you understand what is a junction box is and get the best possible junction box for yourself without any struggle when you need one. Follow the instructions, and you’ll soon find a reliable junction box!
sheet metal parts design guidelines|basics in sheet metal design