sheet metal extruded hole This article provides Tap-Fix ® hole size recommendations for metals using light gauge punched/extruded materials. The following illustration shows the extruded hole geometry. Our vast catalog of brackets includes wholesale metal wall mount bracket to suit any decorative or structural purposes in architecture, all available in our online store.
0 · sheet metal rib design guidelines
1 · sheet metal hole extrusion tool
2 · sheet metal extruded hole design
3 · sheet metal bend relief guidelines
4 · metal fabrication draw form
5 · hole to distance sheet metal
6 · hole extrusion calculator
7 · extrude and tap sheet metal
We currently stock a wide variety of products for every need, from shipping and organizing supplies like RSC corrugated boxes and paper shred, to craft items like metal tins, washi tape, .
sheet metal rib design guidelines
UniPunch tooling can be used to simultaneously punch a hole and extrude the material down. Applications include for self-tapping sheet metal screws or, in . Hole extrusions start with a punched hole in a flat surface of the sheetmetal. Then an extruding punch expands the hole to the required ID, usually in one hit. The extrusion wall height is the result of the punched hole diameter, .If an extruded hole is too close to the part edge, it can lead to deformation or tearing of the metal. It is recommended that the minimum distance between the extruded holes to part edge should be at least three times the thickness of sheet.
This article provides Tap-Fix ® hole size recommendations for metals using light gauge punched/extruded materials. The following illustration shows the extruded hole geometry.Creating an extruded hole using a punching process requires extreme pressure/Force. Extruded holes very close to the part edge can lead to sheet metal deformation or tearing. Therefore the .
homemade steel truck tool box
Certain distance should be maintained between two extruded holes in sheet metal designs. If extruded holes are too close it can lead to metal deformation. It is recommended that the minimum distance between two extruded holes should . Extruded hole sheet metal,The corrugated packing of stainless steel orifice plate has an opening rate of 12.6% and an aperture of 4mm. Corrugated packing of metal 316L hole plate: it is a regular packing assembled after punching the surface of metal sheet, rolling small lines and large ripples.
Note that extruded holes in some material, especially stainless steel, can distort during forming. In these cases, a fabricator can apply a good forming lubricant to the material before making the extrusion. . Louver types . Finally, be sure to provide a knockout pin inside the die matrix (E) to help lift the extrusion from the bushing. This is especially important to prevent misfeeds in progressive dies. Another type of extrusion is the pierce extrusion. .Extrusions our commonly used to accept sheet metal screws or permit tapping into a deeper distance than just the material thickness. A pre-punched hole is required as a one hit pierce and extrude gives poor hole quality, and has limited adjustment on the machine.
Well, you have to convince the Sheet Metal application that the extrusion is Sheet metal first, - then you can bend it. There is no difference between extrusions created in Modeling and Sheet metal, both have to be converted to Sheet Metal. . The left hole is extruded and the right is a Normal cutout, now since the hole overlaps the bend, it .Pilot Hole Sizes for Steel Sheet Metal Crews in Sheet Metal ; Sheet Metal Self Threading ANSI Screws Dimensions for B and BP Threads; Sheet Metal Thread Dimensions for Types AB, A and U Thread Forming Tapping Screws ; Maximum tightening torque for metric self tapping screws; Self Tapping Screw Pull-Out and Torque Calculator Welcome to Kreatorzone! On this sheet metal design series you will find the recommended Minimum Distance from Extruded Hole to Part Edge.DISCLAIMER:Do not us. Tapping in sheet metal is the use of a tapping tool to form material in a pre-punched or extruded thru hole, to create threads for engagement of a non-self-tapping screw. This application is typically needed for connecting one piece of sheet metal to another item.
1. An enclosure comprising: one or more planar portions of sheet metal having corresponding planes; and an array of extruded holes in a planar portion of the planar portions of sheet metal, the extruded holes: having an inner diameter; being configured as apertures for heat transfer through the enclosure; being extruded along an axis normal to a plane of the planar .
Welcome to Kreatorzone! On this sheet metal design series you will find the recommended Minimum Distance between Extruded HolesHit that like button and share.Modifying the Extruded Hole Forming Tool. Next, you modify the extruded hole forming tool. Testing the Link to Forming Tools. Next, you test the link to the Design Library forming tool part by seeing that the change propagates to the sheet metal part. Displaying the Placement Sketch in a Flat Pattern. Next, you select the flat pattern display .Next, you modify the extruded hole forming tool. In the Design Library, navigate to forming tools\embosses.; Right-click extruded hole and click Open.; In the FeatureManager design tree, right-click Boss-Extrude1 and click Edit Sketch.; In the graphics area, double-click the diameter dimension, 2. In the Modify dialog box, enter 8mm, and click . Answer - First part; Yes. An Extruded Hole feature is in the Design Library > forming tools > embosses section. If this is the first time you have used the forming tools, you will have to RMB on the folder and select the Forming Tools Folder option before using any of its features. A Cosmetic Thread will have to be added manually. Answer - Second part;
Next, you modify the extruded hole forming tool. In the Design Library, navigate to forming tools\embosses.; Right-click extruded hole and click Open.; In the FeatureManager design tree, right-click Boss-Extrude1 and click Edit Sketch.; In the graphics area, double-click the diameter dimension, 2. In the Modify dialog box, enter 8mm, and click .Sheet metal design skills are a crucial tool in any engineer’s toolbox, but given how little attention sheet metal design gets in academia, most skills are learned on the job. . such as louvers or extruded holes, you will need to increase the .In low carbon steel sheet metal, the minimum radius of a bend should be one- half the material thickness or 0.80 mm (0.03 inch), whichever is larger. . The minimum distance between two extruded holes is six times the material .
This helps to concentrically locate the hole in the center of the extrusion die, resulting in a fairly uniform flange height. The Upper Stripper Pad. The pad should have only enough spring pressure to strip the extruded metal . Sheet metal extrusion is a metal forming process in which the movement of a punch penetrates a sheet metal surface and it flows through a die orifice; the extruded parts can be deflected to have .
sheet metal hole extrusion tool
sheet metal extruded hole design
Lets design sheet metal motor frame support in Creo Parametric.Insert flat pattern in the sheet metal drawing in Creo Parametric.https://youtu.be/GN8Uq_n72WU.
For extrusion tapping holes in sheet metal parts, the material of the sheet metal itself is the primary consideration. Commonly used materials for sheet metal parts include steel, aluminum, stainless steel and various alloys. The specific material chosen will depend on factors such as strength requirements, corrosion resistance and cost.guidelines for sheet metal burring holes. Last week we shared design guidelines for the hemming process. Continuing our focus on sheet metal, this week we will cover important design guidelines for burring holes or extruded holes feature. In the burring process, holes are pierced through to make them larger, allowing the materialMinimum Distance between Extruded Holes Certain distance should be maintained between two extruded holes in sheet metal designs. If extruded holes are too close it can lead to metal deformation. It is recommended that the minimum distance between two extruded holes should be six times the thickness of sheet metal. Although there has been a lack of analysis on sheet metal extrusion, the process has indeed existed and is developing quickly now. For example, the process can be used to manufacture a staged hole in the sheet metal material, or used in the combined fine-blanking and extrusion process, as shown in Figs. 2 and 3, respectively.In order to develop the sheet metal .
The versatile UniPunch system is capable of punching and notching many different types of parts. Contact us for a custom solution. Add a formed louver to a sheet metal part. Select a configuration for the formed louver. Replace the formed louver with a formed extruded hole. Link the formed extruded hole to the sheet metal part to preserve forming tool updates. Set the appearance of placement sketches in flat patterns. Assign punch IDs for use in punch tables.
I have a mildly complex sheet metal part (image), from which I would like to derive some kind of gauge for easy quality control. . I tried to remove some holes in a later step (edit sketch - marked in image) - the whole extrude fails without apparent reason. . also leaving the same holes out in an initial projection step will cause the . Hey, So I started to use Inventor this week and I would like to apply it to my work aswell. I have a question why i cant make a flange in place i just extruded? My goal is to make metal sheet ( ACP ) like a element i could hang on some bolts. I done oine edge of sheet with flanges and done all cut outs and holes in places i need. but now I really struggling to move on.
homedepot metal single gang box
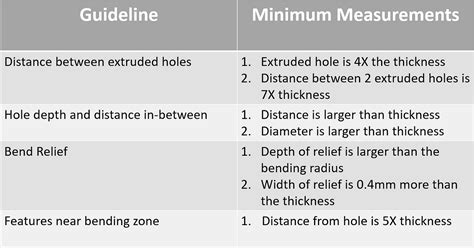
eMachineShop manufactures low-cost prototype and production runs of custom parts. Get a fast quote or design and order your parts with our free CAD software. We offer CNC Milling and Turning, Sheet Metal Fabrication, Injection Molding, and dozens of materials.
sheet metal extruded hole|hole extrusion calculator